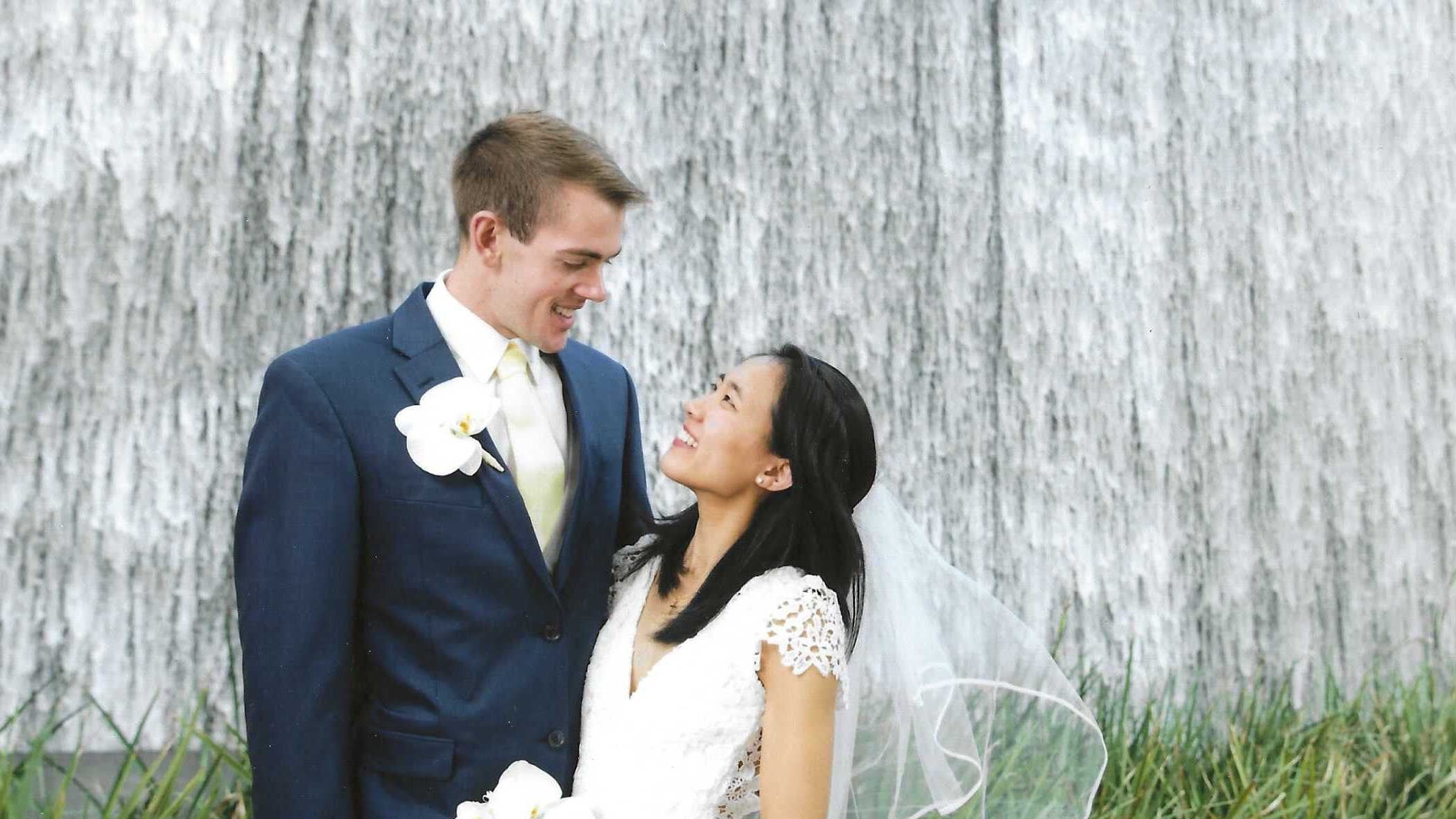
Founded to solve two problems
Tailored Rings
1) Poor fitting and less safe rings.
2) Funding Tailored Alloys to research and develop laser-powder bed fusion additive manufacturing (3D printing with lasers!).
Hunter Taylor set about designing a ring that could open to bypass the knuckle, using the skills and knowledge he’d gained while earning his doctorate at the University of Texas at El Paso’s W.M. Keck Center for 3D Innovation. Hunter produced the first stainless steel versions of “The One” in 2020, and distributed them to friends for testing.
Hunter iterated the ring dozens of times - we’ve lost count - but some highlights include the Titanium version, and built-in sweat grooves. These rings were honed to click better, wobble less, print better, and generally enhance the premium experience. Dozens of versions, thousands of hours of design time, and untold sums were spent to make the ring today. With an exceptional product, we undertook adding black to the collection.
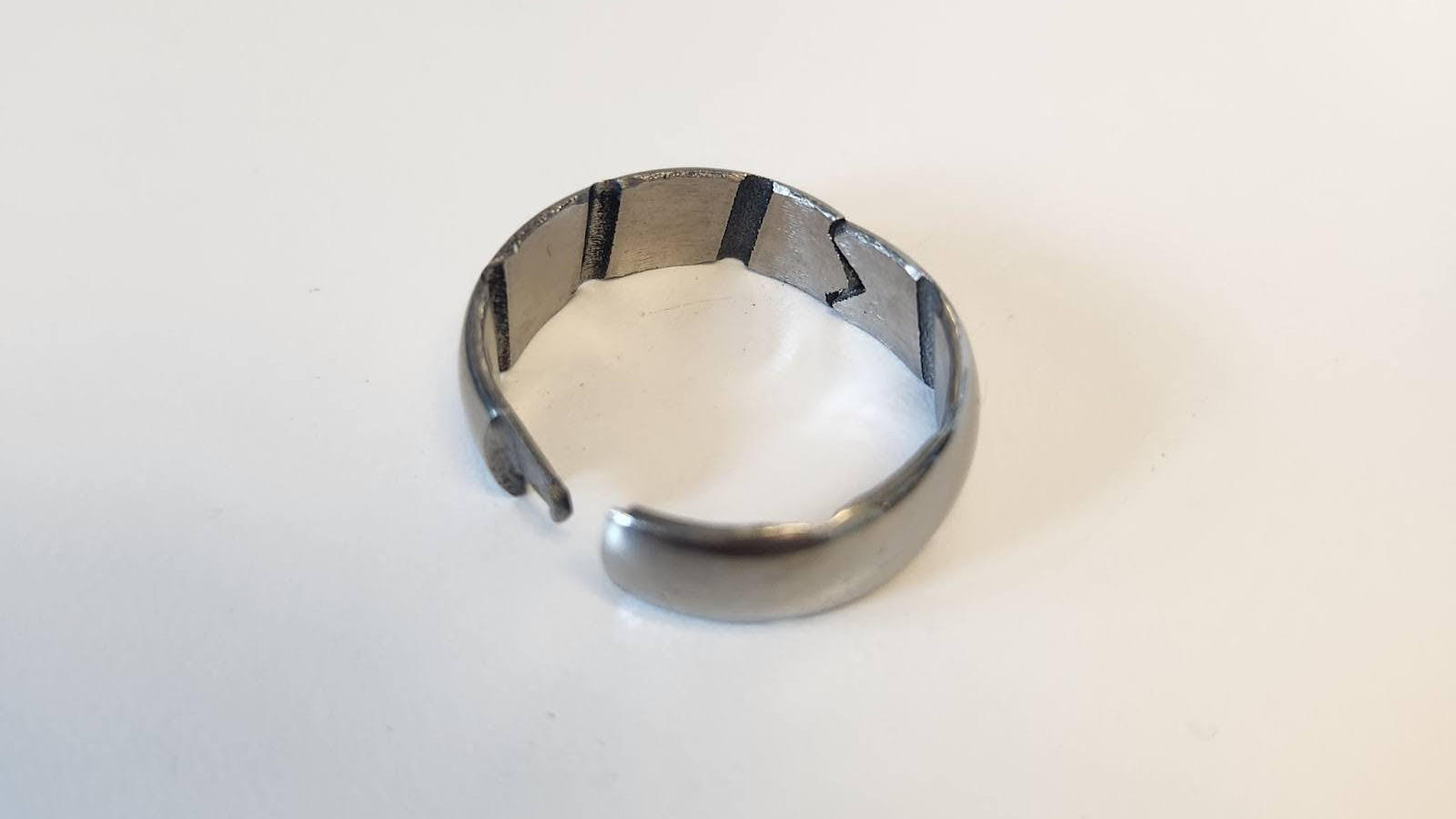
Despite the superior design, he quickly learned that the combination of development and marketing needs for a ring company would not allow it to pay for anything over at Tailored Alloys. It turns out people don’t just buy rings because they’re technically superior!
Nonetheless, a happy synergy remains to this day. Alloys research and manufacturing know-how helps Tailored Rings, and the rings can be studied for future improvements in 3D metal printing. Tailored Rings doesn’t fund Tailored alloys (quote the opposite!) but the partnership is alive and well.
Quality is guaranteed
Each ring is hand finished and tested to ensure it meets our high quality standards.
Process mastery: Countless iterations of 3D printed rings ensure that they come out ready to be hand finished
Craftsman’s Touch: Each ring is carefully inspected and put through a series of tests to ensure it will last a lifetime, fit perfectly, and never fall off.
These standards, along with our process control and materials selection, allow us to guarantee.
We also are able to provide a custom design quote upon request.
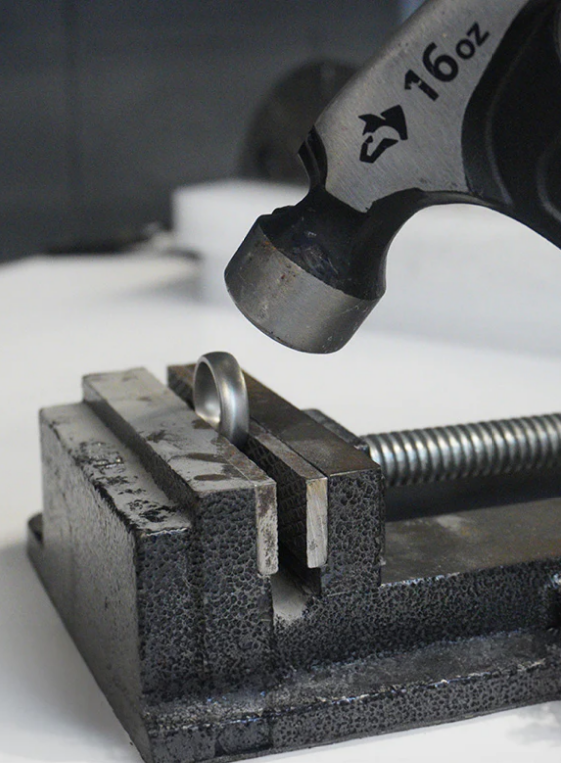
Tailored Rings are made from high performance alloys
CoCrMo, short for Cobalt-Chromium, with a touch of Molybdenum, is a high-performance alloy that's used in things like orthopedic implants and jet engines. It looks as good as platinum or white gold but is tougher against scratches and much stronger. That’s why CoCrMo is awesome for wedding bands. It's super durable, resistant to wear and corrosion, and it won't irritate your skin either.
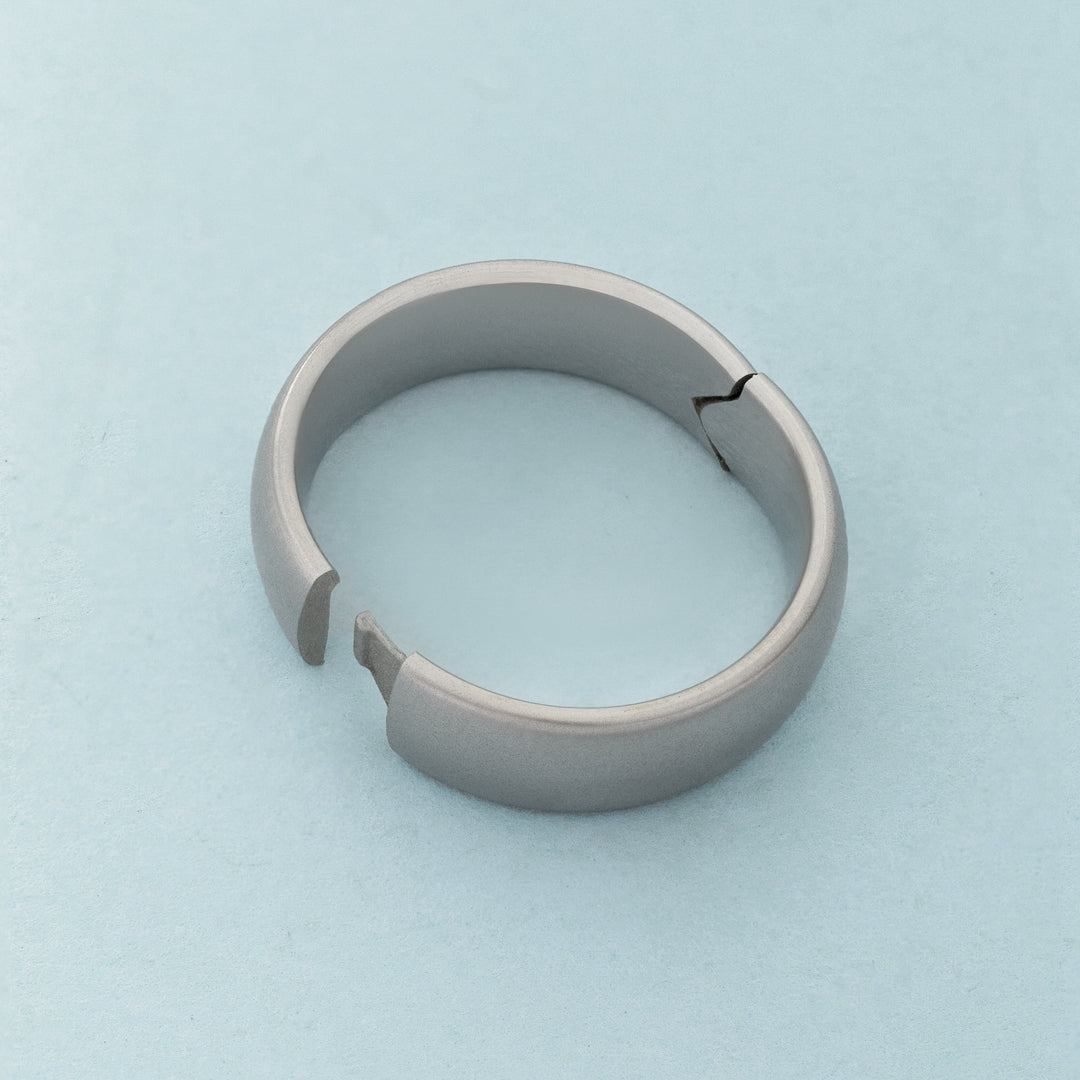
What sets us apart?
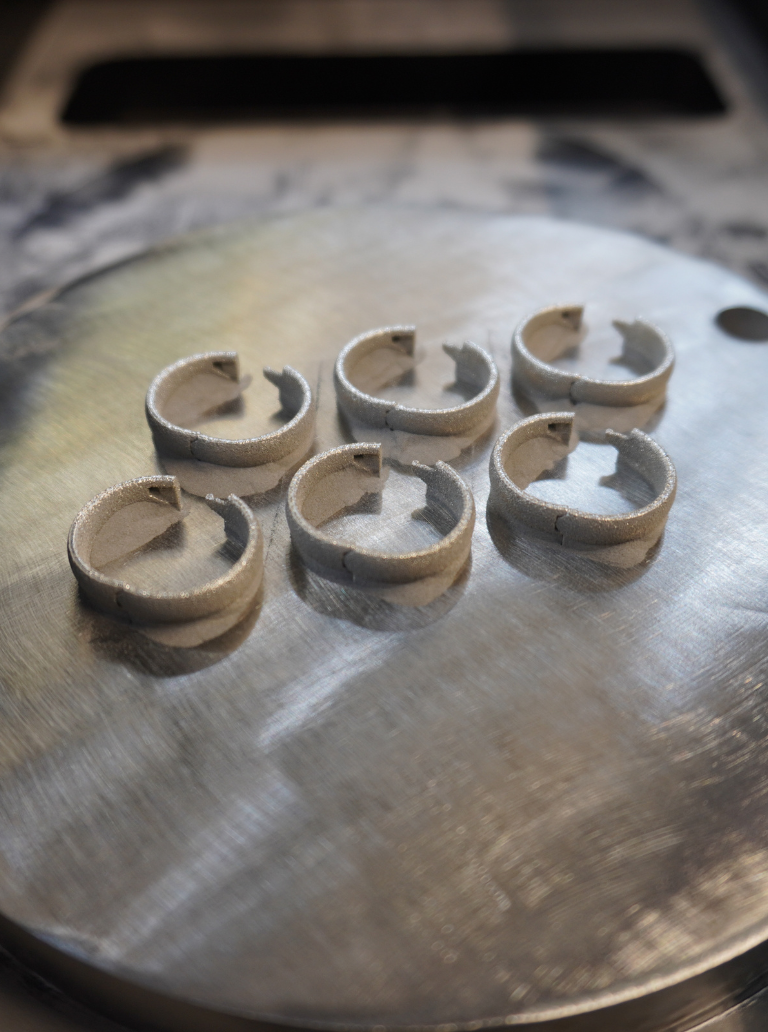
Innovation
From the first sketch to the last polish, Tailored Rings is all about pushing the boundaries of ring design. Our team is dedicated to revolutionizing how rings are made by focusing on top-notch engineering, custom fits, and standout looks. Every Tailored Ring tells your personal story and is built to last with precision engineering. We're always innovating with new materials and hinge techniques to lead the ring industry.
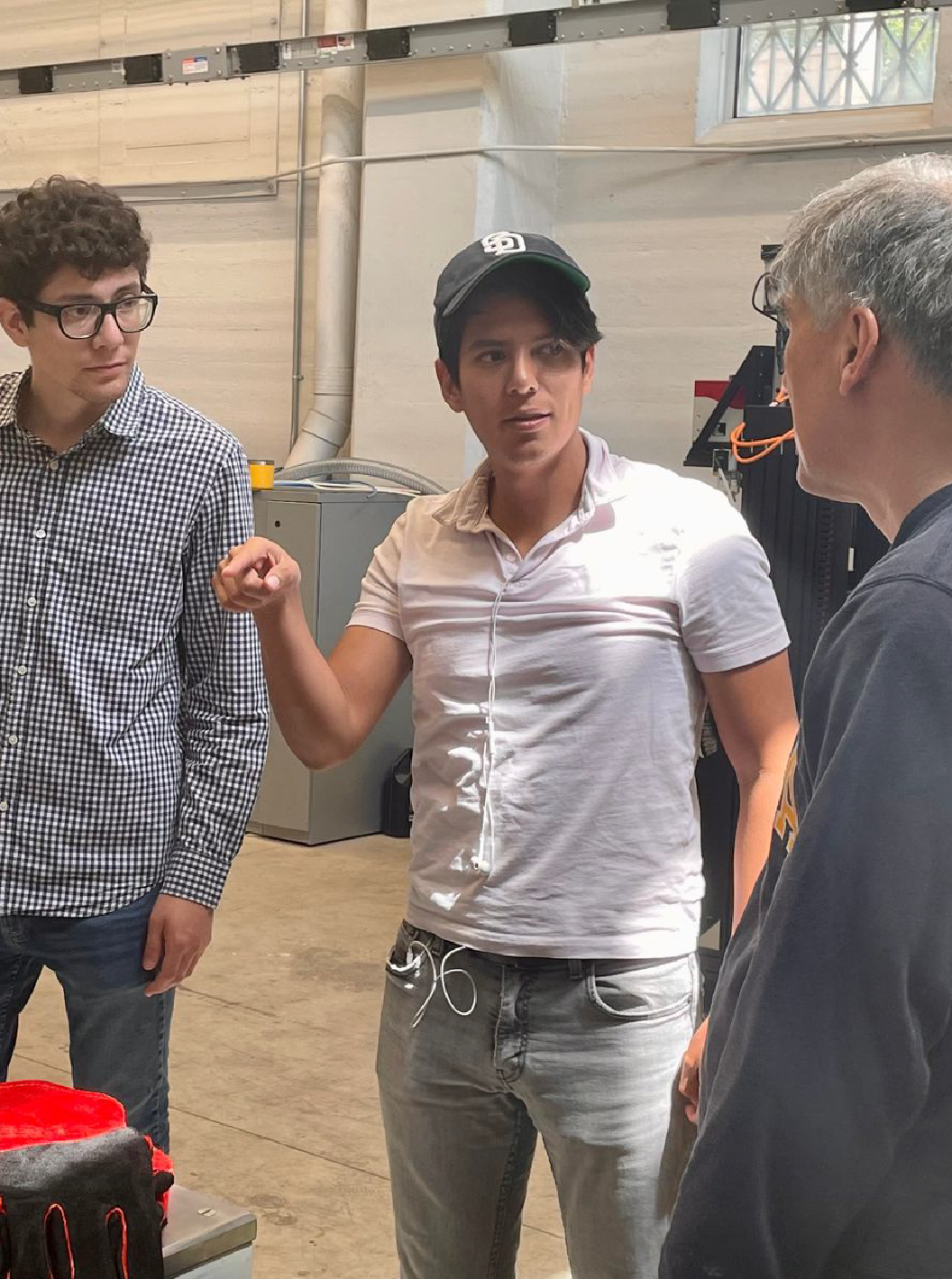
Expertise
Every day at Tailored Rings, our artisans mix old-school craft with new-school tech in our modern workshops. We're experts at making rings that fit perfectly around your finger, not just over your knuckle. We focus on ergonomic design so every ring snaps open and shut satisfyingly, giving you comfort and security. Our skilled craftsmen use advanced methods to create rings that represent strength and commitment.
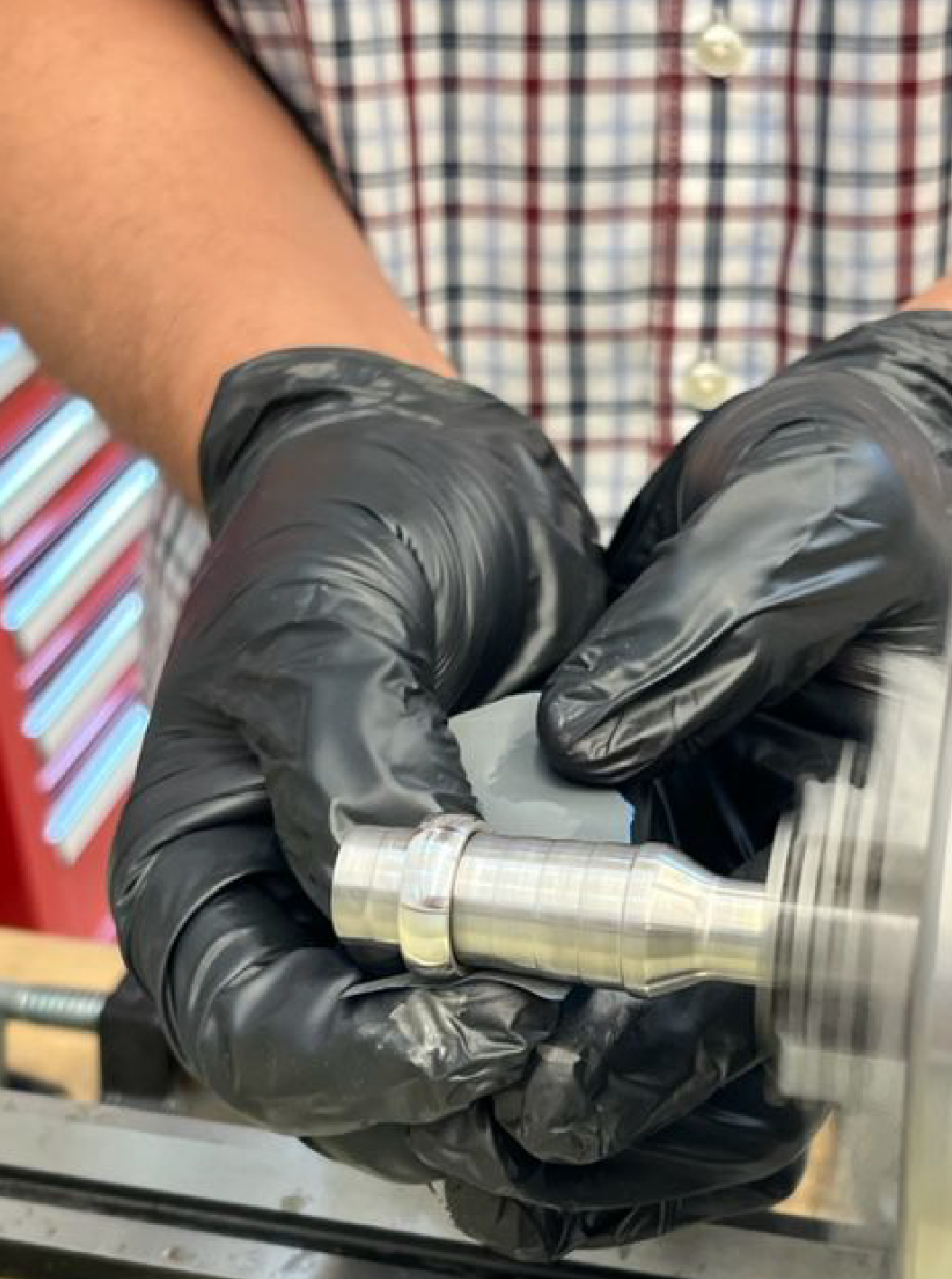
Craftsmanship
Tailored Rings' craftsmanship is all about quality legacy. Our Cobalt Chrome rings are the result of blending traditional craftsmanship with modern precision. Each piece showcases the skill of our artisans, who pay close attention to every detail. We have strict quality controls to make sure your ring is not just a symbol of love but also a durable masterpiece. This commitment to excellence is part of everything we do, from initial design to the final product.